HSK GUILLOTINE SHEARS
//
Three various shear sizes for different cutting lengths and sheet metal thicknesses.
HSK/L/G/W / HSK/N / HSK/S
Guillotine shears made by HSK are stand-alone, motor driven machines with electrical control mostly used for cutting or trimming flat sheet metal.
It is also possible to cut other various materials like plastics, CFRP/GFRP, fleece material, foam or precious metals, mainly in form of sheets, but also formed work pieces like deep‑drawing parts and profiled sheet metals or directly from a coil.
Depending on the requirements concerning cutting length, cutting force and cutting speed, the shear drive is realised either by a strong bevel gear motor or by a AC-motor, fly‑wheel and clutch-brake-combination – in special cases also by a servo motor.
We differentiate between the three various shear sizes HSK/L/G/W, HSK/N and HSK/S which are manufactured for different cutting lengths and sheet metal thicknesses. Hereby the customer is able to choose the most fitting HSK-guillotine for his purposes.
GUILLOTINE SHEARS
FOR PLATE PRODUCTION
For the production of printed aluminum or steel plates, a special guillotine shear with a motor driven front stop has been developed. This guillotine shear cuts plates with the required precision, that means maximum accuracy as well as minimal burr formation and distortion.
Shears for plate production cut with rates up to 30 cuts per minute or more, according to the plate dimensions. Because of that, usually the dive unit is realized with a clutch-break-combination, but also converter controlled AC motors or servomotors can be used.
TRIMMING SHEARS
FOR DEEP-DRAWN PARTS
In process of manufacturing plastic deep-drawn parts, the border zone has to be removed after the deep-drawing process which is usually realized with exact milling. However, the deep-drawn part can only be stress-free milled after the border zone where the component was clamped got removed beforehand.
To trim the border of deep-drawn parts before milling, a special eccentric shear has been developed.
GUILLOTINE SHEARS FOR
CUTTING DIRECTLY OF A COIL
To meet customers demand, our guillotine shears can be modified to cut sheet metal or plastic directly of a coil, instead of realizing this with a very expansive production line. Therefore, a coil holder is mounted in front of the shear and a feeding unit is integrated into the special manufactured shear table.
The control of the guillotine shear is accordingly extended with a positioning control unit to program variable feed lengths. The drive unit of the feed roll can be realized with an AC gear motor or servo motor accordingly to the required performance. The length measurement is realized with a suitable rotary encoder.
GUILLOTINE SHEARS FOR CORRUGATED- & TRAPEZOIDAL SHEET METAL
Corrugated and trapezoidal sheet metal is manufactured in long production lines by roll forming. A strong punch cut then cuts the sheet metal into standard sizes for example lengths of 15 m. Therefore, it is usually unavoidable to make up the sheet metal webs.
For this purpose, a special section shear has been developed which allows to cut the already formed sheet metal to length. This machine works like a normal guillotine shear with a slanted cut, compared to a punch cut, in order to cut the profiled sheet metal with lower shear forces and noise emissions. The upper and lower blades are formed according to the shape of the formed sheet metal, as well as the hold down and plastic on the shear table.
THE PERFECT CUT
FOR A WIDE RANGE OF MATERIALS
HSK EQUIPMENT
//
We offer you an extensive range of standard and special equipment for all HSK guillotine shears.
We would also be happy to support you with individual requirements..
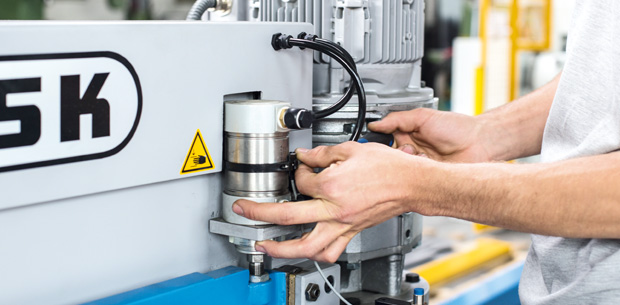
STANDARD EQUIPMENT
- Side frames manufactured using vibration-damping cast iron
- Shear table with continous flat supporting surface
- Table stop with measuring tape, length 600 mm type HSK/L/G/W, length 1000 mm type HSK/N and HSK/S
- Two table extensions with T-slots, length 450 mm type HSK/L/G/W, length 650 mm type HSK/N and HSK/S
- Spring-actuated hold down manufactured in one piece, with glued-in rubber cord, mechanically linked with movement of cutter bar
- Rigid finger protection in front of the hold down (only necessary if hold down opens more than 6 mm)
- Steel blades produced in one piece, with four cutting edges and wedge angle 90°, using special blade steel
- Manual cut gap adjustment by fine threaded spindles at the front of the left and right side frame, clamped by hexagon screws at the side frames, for adjustment after changing or turning the shear blades
- Milled horizontal surfaces at the side frames for precise levelling of the machine
- Manually actuated back stop using gear rods, with measuring tape, length 500 mm type HSK/L/G/W, 600 mm type HSK/N and HSK/S
- Cut release by movable foot switch
- Sheet metal chute at the backside of the machine
- Sidewise safety guard ending 1200 mm behind the danger area “shear blades“ according to DIN EN 13985 Safety of Plate Shears, height of safety guard approx. 1400 mm according to DIN EN 294 tabular 1
- Dual-trace safety light barrier according to DIN EN 13985 Safety of Plate Shears
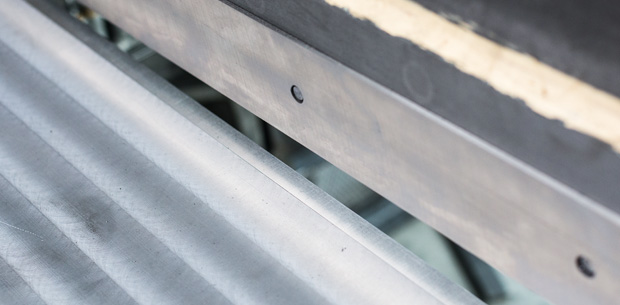
SPECIAL EQUIPMENT
- Shear table covered with plastic plates and optionally with integrated brushes, designed for sheet metal with easily scratched surface
- Oil central lubrication, manually or automatically actuated
- Special blades for cutting stainless steel, sheet metal for transformers, plastics, rubber, etc.
- Cut illumination integrated in the shear cover, for cutting using a mark on the sheet metal
- Pneumatically acutated hold down, for adjustment of the contact pressure and the moment of lowering and lifting
- Foldaway finger protection in front of the hold down
- Manual cut gap adjustment by fine threaded spindles and two levers with locking bolts at the front of the left and right side frame, clamped by hexagon screws at the side frames, for adjustment depending on the sheet metal thickness
- Mechanical stroke counter
- Mounting feet or precision wedge shoes for comfortable and vibration-damping installation
- Customised base frame
- T-slot at the front side of the table for adjusting stops and table extensions
- T-slots in the table e.g. for adjusting table ruler and tilting stops, the number can be freely selected
- Table ruler as a rigid front stop
- Special table stop (TTA) with tilting stop, manually adjustable, length up to 3000 mm, also available with a digital position indicator
- Special table extensions (TTV), length up to 3000 mm
- Spring-actuated tilting stops for T-slots in the table extensions or in the shear table
- Angle stop (WA500) mounted on the shear table, length 500 mm, manually actuated, +/- 60°
- Motor-driven precision front stop with threaded spindles (VA), length 750 mm, with position control, drive by stepper motor
- Motor-driven back stop with gear rods (ZA), length 800 or 1000 mm, with position control, drive by AC-motor and frequency converter
- Motor-driven precision back stop with threaded spindles (GA), length 800 or 1000 mm, with position control, drive by AC motor and frequency converter or stepper motor
- Cut release by selectable contacts integrated in the stop bar of the back stop
- Support for thin sheet metal by pneumatically actuated supporting fingers, length 140 mm
- Horizontal sheet metal support
- Sheet metal support by pneumatically actuated tilting table with rolls
- Conveyor belt with integrated pneumatically actuated sheet metal support, scrap gate and scrap box
- Conveyor belt mounted on scissors lift, for supporting and transporting the sheet metal
Additional customisation on demand. |